Company History
-
1952
-
1956
- 1957Successful development of steel powder by nitriding pulverization.
- 1958Production and marketing of sponge iron made from iron ore by direct rotary kiln reduction process.
- 1960Company was renamed Nippon Special Iron Powder Co., Ltd.
Commenced trial production of spherical iron powder. - 1961Development of oxidization process for surface-treating iron powder. Marketing of toner carriers for electrophotography using the technology with the spherical iron powder developed in the previous year.
- 1963Launched marketing of iron powder for powder metallurgy.
-
1966
- 1968Marketing of spherical iron powder improved for facsimile machine.
Volume production of iron powder, TC-24, for powder metallurgy. -
1970
- 1972Simultaneous production method developed for sponge iron and activated carbon.
- 1974Acquisition of adjacent land (10,000m²) owned by the national government
- 1975Develops technology to shape irregular type carrier into flat shaped carrier or spherical carrier.
- 1977Full-scale production and marketing of iron powder for powder metallurgy with improved compressibility.
-
1979
- 1981Enhanced production capabilities for iron powder carrier.
- 1982Perfected ferrite carrier for practical application.
-
1984
wrinkletype smoothtype
Full-scale production and marketing of ferrite carrier for electrophotography. - 1985Added a plant site in Takahagi city, Ibaraki.
- 1986Trial production of oxygen absorber (WonderKeep®) commenced.
-
1988
- 1989 Company was renamed Powdertech Co., Ltd., with the capital increased to ¥585 million.
- 1990Company made public offering on the OTC(Over the Counter) stock market operated by Japan OTC Securities which was owned by Japan Securities Dealers Association.
Capital increased to ¥1,557 million. - 1991Completed Takahagi Plant (for WonderKeep®).
Established PTS, a wholly owned subsidiary. -
1995
Enhanced the production capabilities for ferrite carrier. -
1996
- 1997Completed a plant exclusively for the EF ferrite carrier.
-
2002
Established Powdertech International Corporation, a wholly owned U.S. subsidiary for international sales and marketing.
Company wholly owned Musashi Sangyo Co., a trading house for the domestic Market.
All the business units were ISO9001 certified. -
2003
Spun off the oxygen absorber business into a newly created Wonderkeep Takahagi Co., a wholly owned manufacturer of WonderKeep®. - 2004Company was listed on JASDAQ, a securities exchange, operated by JASDAQ Securities Exchange Inc, which originated with Japan OTC Securities.
Launched a company-wide Total Productive Maintenance (TPM). - 2005Enhanced the EF ferrite carrier production capability to 400 tons monthly.
- 2006All the business units were OHSAS 18001 certified.
- 2007Company was awarded Excellence TPM Award to finish the movement.
Selected by The Ministry of Economy, Trade and Industry (METI) as one of the “300 Strongest Small-Medium Sized Enterprises”. - 2010As a result of acquisition of JASDAQ Securities Exchange Inc., by Osaka Security Exchange Co., Company was listed on JASDAQ market operated by Osaka Security Exchange.
As a result of smaller stock markets integration by Osaka Security Exchange, Company was listed on its Standard Section on JASDAQ market.
Acquired an adjacent plant site (9,000m²). - 2013Due to creation of Japan Exchange Group (JPX) from the merger of the Tokyo Stock Exchange group and Osaka Securities Exchange Co., Company was listed on JASDAQ Standard Section operated by Tokyo Stock Exchange Inc., owned by JPX.
- 2014Company absorbed by merger Musashi Sangyo Co., a wholly owned domestic sales arm.
-
2015
- 2016Marks the 50th anniversary of the founding of Powdertech.
-
2017
Changes the number of shares per share unit from 1,000 to 100, and consolidates its common shares on basis of one for every five shares.
Selected by METI as one of the “Companies Driving Regional Growth”. -
2020
- 2022PTS,non-consolidated wholly-owned subsidiary, is dissolved and Powdertech takes over all operations.
Transferred to the Standard Market on the Tokyo Stock Exchange following a market segments restructuring by Tokyo Exchange Market, Inc.
Withdrawal from iron powder sales business.
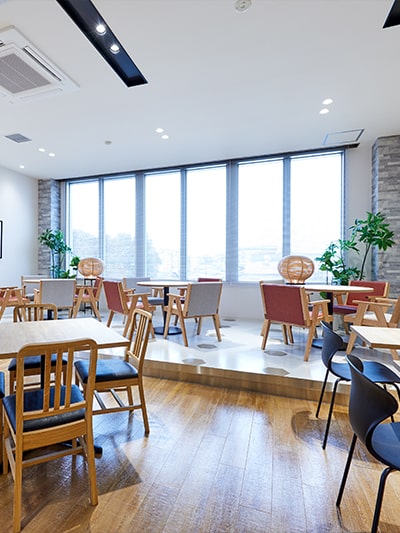
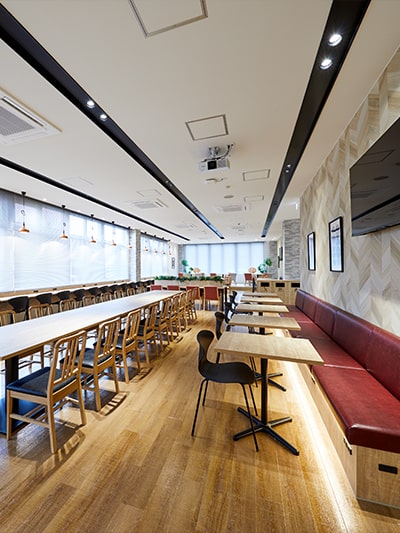
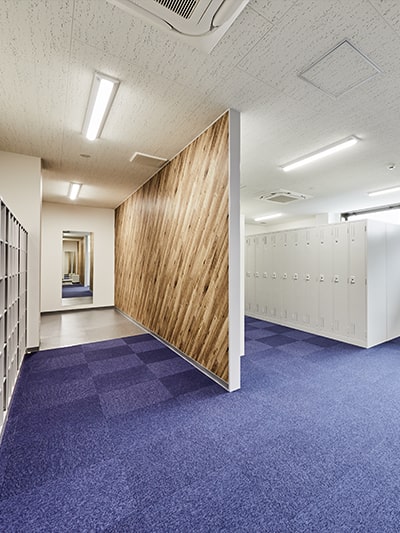
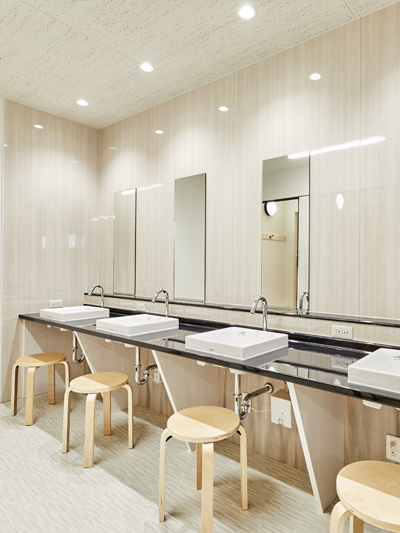
Evolution of Our Technologies
Iron powder | Carriers for electrophotography | |
---|---|---|
Founding Years |
1947: Start of basic research on iron powder (activated iron) 1952: Company’s launch as Japan’s only manufacturer specializing in iron powder Research on activated iron: Research on highly activated iron powder by refining iron at low temperatures Hokuriku Kako Co., Ltd. (predecessor to Powdertech) was established as a groundbreaking venture company and it began manufacturing iron powder at full scale and selling activated carbon (a byproduct of the iron powder production process). |
|
1950s |
1956: Company moved to Kashiwa City, Chiba Prefecture The company succeeded in developing steel powder using a nitriding and pulverization method and succeeded in producing sponge iron by direct reduction in a rotary kiln using acid sludge and iron ore as raw materials. Based on these technologies, iron powder products with enhanced functionality were developed and put on the market. ✦ For powder cutting (1956) Joint research was conducted with the Technical Research Institute of the Ministry of Transport on iron powder for stainless steel cutting. Sales of iron powder for cutting in continuous casting were expanded to various companies. ✦ For welding rods (1957) Iron powder with improved insulation properties was developed by coating iron powder particles with a thick film of iron oxide, applied to welding rods used in shipbuilding, etc. ✦ For recovery of precipitated copper from copper mines (1958) Developed jointly with the Department of Mining, Iwate University. Iron powder with high-yield recovery of precipitated copper was developed by combining a buddle with wet magnetic separation. ✦ Chemical reduction (1958) A market was developed for reducing agents in the production process for dye intermediates. ✦ For drilling and fusing (iron powder lance) (1959) Iron powder and oxygen passed through a steel pipe with an inner diameter of 10-15 mm are ignited and sprayed out the tip to drill and fuse concrete or rock. Used for repairing railroad bridge piers made of concrete, repairing steel mill furnaces, etc. |
|
1960s |
✦ Iron powder for magnetic flaw detection (1961) Iron powder for magnetic flaw detection was developed with a violet-colored oxide coating on the surface of the iron particles. ✦ Conmix cement strengthening agent (1963) Concrete with a 10-20% admixture of iron powder as the main ingredient was developed through joint research with the Building Research Institute of the Ministry of Construction, the Tokyo Office of the Kanto Regional Construction Bureau, and major construction companies. The strengthening agent had extremely high early strength and was indispensable to Japan’s construction boom during its rapid-growth era. ✦ Iron powder for powder metallurgy (1964) After long research and development beginning in 1958, iron powder for powder metallurgy was put on the market. |
Development began on carriers for electrophotography. We developed the technology to coat the surface of spherical iron powder (which is lighter and has more fluidity than steel beads) with nickel, copper, etc., as a carrier for the magnetic brush developing method. This technology was provided to the Electrotechnical Laboratory of the Agency of Industrial Science and Technology under the Ministry of International Trade and Industry (MITI) and opened the door to today’s electrophotographic carrier technology. Our surface oxide coating technology for iron powder for magnetic flaw detection later became an important processing method to control two-component carrier conductivity in plain paper copiers (PPCs). We then embarked on joint research and development with six companies, including a camera manufacturer and a paper manufacturer, and in 1967 brought to market an iron powder carrier (steel flat carrier) for facsimile machines. |
1970s |
Iron powder was developed for disposable hand warmers using the heat generated from the oxidation reaction and put on the market.
![]() ![]() |
In 1970, iron powder carriers for plain paper copiers (PPCs) were developed and put on the market. Subsequently, we developed and launched iron powder carriers with various shapes and surface properties based on sponge iron powder obtained from direct reduction in a rotary kiln and steel-based flat iron powder. In these ways, the mechanical processing technologies cultivated in the iron powder business were applied primarily to improve developing properties by refining the magnetic brush shape. The electrical resistance of early iron powder carriers was adjusted by coating the surface with an oxide film.
![]() ![]() |
1980s |
In 1984, we began research and development on oxygen absorbers, and in 1986 we began selling our first in-house brand of oxygen absorber, WonderKeep®. While selling these oxygen absorbers, customers requested a type that would visually indicate the presence or absence of oxygen, so in 1987 we started selling a prototype of our WonderSensor® oxygen detector. Up to that point, oxygen sensors had been in the form of tablets, while we developed a sensor in sheet form. This new form offered customers greater flexibility for use and eliminated the feeling of inserting a foreign object. |
Sales of iron powder carriers peaked in the 1980s. Iron powder carriers are characterized by low electrical resistance and high relative density. For this reason, they were not able to properly meet the requirements of the market at the time for high image quality and durability. We began developing ferrite carriers, a material with lower relative density and higher resistance than iron powder, and in 1983 we developed a commercially viable Cu-Zn ferrite carrier. The high durability and high image quality produced by Cu-Zn ferrite carriers led to their adoption in place of iron powder carriers. ![]() ![]() |
1990s |
![]() ![]() ![]() ![]() |
We started developing environmentally friendly ferrite carriers (EF carriers) that do not contain heavy metals in order to comply with environmental regulations under California law in the United States, and commercialized Mn-Mg-Sr ferrite carriers and Li-Mg-Ca ferrite carriers in 1996. This move wound up replacing Cu-Zn ferrite carriers with EF carriers.
![]() New resin coating technologies have also been developed and commercialized. Previously, the properties could only be controlled by the base resin and core material, but now, various additives are used to adjust and improve charging properties, electrical resistance, environmental characteristics, durability, and other properties. Coating methods have also been developed and introduced to make effective use of these additives. |
2000s |
To meet the expanding requests of customers, we started to develop new oxygen absorbers, oxygen sensors, and combined products and brought them to market. Oxygen absorbers ✦ Moisture-activated, oil-resistant type (2007) Oil-resistant processing was applied to the conventional moisture-activated absorber casing to accommodate confectioneries with high moisture and oil content. ✦ Miniature type (2007) Small, moisture-activated absorbers were developed in response to a trend toward individual packaging in the food market. Dedicated production machines were introduced and sales were launched. ✦ Metal-detector-safe type (2009) More customers had begun using metal detectors in food inspections to ensure food safety. Since conventional iron-based oxygen absorbers are detected as foreign substances by metal detectors, we developed and launched oxygen absorbers made with organic components instead. ✦ Carbon dioxide-generating integrated type This type was developed to absorb oxygen and simultaneously generate carbon dioxide gas in the same amount as the oxygen absorbed to suppress shrinkage of the packaging bag, thereby preventing the soft confectionery or other contents from being crushed. Oxygen sensors ✦ Improved low-temperature reactivity type (2001) We developed this new type of oxygen absorber to change color rapidly at low temperatures. This product enabled the more efficient evaluation of product quality in winter or low-temperature environments. ✦ Water/oil resistant type (2002) Based on our imperforated water- and oil-resistant oxygen sensor launched in 1998, we developed a smaller type for our combined products. |
As full-color photocopiers and printers went mainstream, the size of toner particles became smaller, and carrier particles along with them, with a standard average particle size of about 35μm. In response to the market’s demand for higher performance and durability, we released many resin-coated ferrite carriers with functionality enhanced by various materials added to the coating resin. Significant changes were also taking place in electrophotographic systems. Up to that point, the only consumable that had to be replenished in the system was the toner, but in the pursuit of more stable image quality, newer systems required replenishment of both the carrier and the toner. As a result, carriers, which used to be a component of the developing equipment, had become a consumable. |